Introduction
Injection molding is a cornerstone of modern manufacturing, enabling the mass production of complex parts with precision and efficiency. This process is integral to producing wide products that span industries from automotive to consumer electronics. Central to the success of injection molding is the careful selection of materials, as the properties of the chosen polymer directly impact the final product’s performance, durability, and aesthetic qualities.
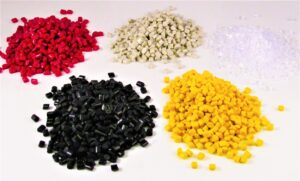
Common Thermoplastics for Injection Molding
Polyethylene (PE)
Due to its versatile properties, polyethylene is one of the most widely used thermoplastics in injection molding.
Types: HDPE and LDPE
- High-Density Polyethylene (HDPE): Known for its high strength-to-density ratio, HDPE is ideal for applications requiring durability and chemical resistance.
- Low-Density Polyethylene (LDPE) Offers greater flexibility and is used in applications with a softer material.
Properties:
- Chemical Resistance: HDPE and LDPE resist many chemicals, making them suitable for containers and packaging.
- Low Cost: Polyethylene is inexpensive, making it a cost-effective choice for high-volume production.
- Ease of Processing: Its processing properties allow for efficient molding cycles.
Applications:
- Packaging: Commonly used in bottles, containers, and bags.
- Toys: Utilized in the production of safe, durable toys.
- Containers: Widely used in food and chemical storage due to its inert nature.
Polypropylene (PP)
Polypropylene is another essential thermoplastic known for its balance of properties.
Properties:
- Rigidity and Heat Resistance: PP maintains its shape and integrity under stress and high temperatures.
- Low Density: Contributes to lightweight yet sturdy products.
Applications:
- Automotive Parts: Used in bumpers, dashboards, and other components.
- Household Items: Found in furniture, containers, and appliances.
- Medical Devices: Utilized for its sterility and resistance to bacterial growth.
Acrylonitrile Butadiene Styrene (ABS)
ABS is prized for its robustness and superior finish.
Properties:
- Impact Resistance: Offers excellent toughness, making it suitable for high-stress applications.
- Rigidity: Maintains structural integrity under various conditions.
- Good Surface Finish: Allows for aesthetically pleasing products with minimal post-processing.
Applications:
- Consumer Products: These are common in helmets, luggage, and kitchen appliances.
- Electronics Housings: Used in computer cases, remote controls, and other electronic enclosures.
Polycarbonate (PC)
Polycarbonate is known for its exceptional strength and transparency.
Properties:
- High Impact Strength: Extremely durable and resistant to physical stress.
- Transparency: Allows for clear and visually appealing products.
- Heat Resistance: Maintains performance at high temperatures.
Applications:
- Safety Glasses: Essential in protective eyewear due to its clarity and strength.
- Automotive Components: Used in headlamp lenses and other transparent parts.
- Electronic Parts: These are found in various electronic enclosures and components.
Polyamide (Nylon)
Nylon is recognized for its combination of strength and flexibility.
Properties:
- High Strength: Suitable for demanding mechanical applications.
- Abrasion Resistance: Resistant to wear and tear.
- Good Thermal Properties: Can withstand high temperatures without degradation.
Applications:
- Gears: Common in mechanical and automotive gears.
- Bearings: Used in applications requiring low friction and high durability.
- Automotive Components: Utilized in various engine and structural parts.
Engineering Plastics for Injection Molding
Polyoxymethylene (POM/Acetal)
Acetal is celebrated for its precision and stability.
Properties:
- Dimensional Stability: Maintains size and shape under varying conditions.
- Low Friction: Ideal for moving parts.
- High Stiffness: Provides strength and rigidity.
Applications:
- Precision Parts: Used in small, intricate components.
- Gears and Bearings: Favored for its durability and low wear.
- Automotive Parts: Utilized in various mechanical applications.
Polyetheretherketone (PEEK)
PEEK stands out for its exceptional resistance and strength.
Properties:
- Thermal and Chemical Resistance: Withstands extreme conditions without compromising performance.
- High Strength: Suitable for high-stress applications.
Applications:
- Aerospace: Used in components that require high performance and reliability.
- Medical Implants: Biocompatible and suitable for long-term implantation.
- Electrical Components: Utilized in high-performance electrical insulation and connectors.
Elastomers and Thermosets
Overview of Elastomers (TPE, TPU) and Thermosets (Epoxy, Phenolic)
Elastomers and thermosets offer unique properties that make them suitable for specialized applications.
Properties:
- Thermoplastic Elastomers (TPE): Combine plastics’ processability with rubber’s flexibility. It is commonly used in flexible seals and over-molded grips.
- Thermoplastic Polyurethane (TPU): Known for its elasticity, transparency, and resistance to oil and grease. Used in applications like footwear and protective cases.
- Thermoset Epoxy: Offers excellent adhesion, chemical resistance, and mechanical properties. Widely used in coatings, adhesives, and composite materials.
- Phenolic Resins: Known for their heat resistance and electrical insulating properties. Used in electrical components and high-temperature applications.
Applications:
- Automotive Seals: TPE and TPU are used for flexible and durable seals.
- Electrical Insulation: Epoxy and phenolic resins provide reliable insulation in electrical applications.
- Consumer Goods: Elastomers are used in various consumer products for their flexibility and durability.
Factors Influencing Material Selection
Choosing the right material for injection molding involves considering several key factors:
Cost
Balancing material cost with performance requirements is crucial for economic viability.
Mechanical Properties
Strength, impact resistance, and flexibility are essential considerations based on the application.
Thermal Properties
Materials must withstand the operational temperatures of the final product.
Chemical Resistance
Ensuring compatibility with the chemicals the product may encounter is vital for longevity.
Aesthetic Requirements
The final product’s appearance, including color and surface finish, impacts material choice.
Regulatory Compliance
Materials must meet industry-specific regulations and standards, such as FDA approval for medical devices.
Environmental Considerations
Sustainability and recyclability are increasingly important in material selection, driven by environmental regulations and consumer demand.
Emerging Trends and Future Developments
Bioplastics and Biodegradable Materials
Bioplastics offer a sustainable alternative to traditional plastics, reducing environmental impact.
Nanocomposites and Advanced Fillers
Incorporating nanomaterials can enhance the properties of plastics, making them stronger and more functional.
Recycled and Sustainable Materials
Using recycled plastics helps reduce waste and supports environmental sustainability.
Customized Polymer Blends
Tailoring polymer blends to meet specific performance requirements is becoming more common, allowing for optimized properties in final products.
Conclusion
The selection of materials in injection molding is a critical step that directly influences the final product’s quality, performance, and cost-effectiveness. By carefully evaluating the application’s requirements and considering emerging trends, manufacturers can ensure that they choose the most suitable materials for their needs.